By assisting you to identify the risks and opportunities that are prevalent in your industry or application, NHP can facilitate the required services and solutions to maximise your operational investment in accordance with your priorities and objectives.
NHP Services and Solutions is backed by our supply line partners, both locally and overseas, with genuine spare parts, technical support and training though to on-site service and repairs.
Not only is NHP the long-standing exclusive Authorised Distributor for Rockwell Automation in Australia and New Zealand, we are now also the sole Authorised Service Provider in this region for the automation giant. In conjunction with Rockwell Automation and our other major supply line partners both locally and overseas, NHP offers our customers genuine spare parts, technical support and training though to on-site service and repairs, leveraging industry and technology-specific expertise to maximise operational investments, improve your business and meet your everyday needs.
Together, NHP’s and Rockwell Automation’s teams of service professionals are able to:
- prepare for the future of SMART Manufacturing through The Connected Enterprise, which delivers value by integrating your industrial assets with the rest of your supply chain;
- train workers and augment your workforce to manage knowledge transfer and develop new skills to enable IT/OT convergence, and take advantage of innovative technology;
- prepare for people and asset safety with assessments, engineered offerings, pre-engineered solutions, and a remote audit-and-tracking service to confirm that people follow proper procedures;
- go beyond a ‘keep-it-running’ mindset and make the most of your production infrastructure with asset and plant optimisation services; and
- tap new and expanding information infrastructure and security services to better define, design, deploy, manage and monitor the right network infrastructure for your plant.
The NHP Service and Solutions commitment
NHP has an extensive service infrastructure including Repair Centres, Test Rooms, Field Service Technicians, Application Engineers, and Project Managers. With more than 50 years’ experience in the electrical and engineering industry, our specialist teams work collaboratively to design and deliver solutions to maximise the success of your project.
NHP prides itself on its customer excellence. We are committed to look after our customers for the life of their project and beyond. Our team of service technicians hold tertiary and/or trade qualifications and regularly participate in Supply Line Partner training programs to ensure our services are executed in line with manufacturer specifications. Equipped with comprehensive product knowledge, our technicians are committed to delivering the best practice of electrical services, while providing an exceptional customer experience.
Our capabilities
NHP offers an extensive range of service solutions to suit a wide range of needs, whether your need is for installation and commissioning, migration, emergency breakdown or lifecycle services. From start-ups to conversions, we have the technical expertise to help you increase uptime and optimise equipment performance. Available on an as-required, scheduled or full-time basis, we help you meet your specific needs throughout your maintenance strategy’s lifecycle.
NHP and Rockwell Automation have a network of service professionals throughout Australia and New Zealand who can quickly respond to your needs.
Product application and lifecycle support
Scalable service packages give you greater flexibility in meeting your unique business goals, operational needs or budgetary constraints, allowing for faster downtime recovery, lower maintenance costs, increased visibility on asset obsolescence and easy access to replacement parts.
- On-demand support to address your top challenges and fill skills gaps
- Integrated support to help you stay productive and positively impact your daily operations
- Managed support through customised options that improve performance
Workforce support and training
As the global skills gap threatens to increase plant downtime and slow the speed to market, now more than ever, workforce support and training are key to your success. NHP Services and Solutions provides services to empower your people and extend the reach of your team, at whatever level you require.
Occasionally or frequently, you may encounter situations that need technical expertise outside the scope of your workforce.
- Remediate those situations and minimise unplanned downtime
- Enable your workers and bridge the skills gap
- Supplement your internal capabilities both offsite and on, with the help of subject matter experts
- Optimise your operations by maximising workforce productivity.
People and asset safety
To help you meet production needs safely and achieve regulatory compliance, we offer a complete set of safety services designed around hazardous energy control (including lockout/tagout procedures), electrical safety (including arc flash assessments) and machine safety. We can help by using our solutions in remediation type processes. These services can be provided as consultative assessments, engineered offerings, pre-engineered solutions and a remote audit and tracking system, where we can track whether a given plant or location is adhering to the safety procedures.
- Hazardous energy control - comprehensive lockout/tagout solutions so you can proactively manage employee safety while optimising production efficiency
- Electrical safety services - assisting manufacturers to plan, so they can comply and perform routine maintenance without risking productivity
- Machine safety services - utilising a clearly defined process to help improve safety, by identifying the steps that are required to assess and mitigate machinery risks. With an assessment, we help to evaluate plant risk and support well informed decisions that can improve employee and machine safety. Our thorough review of design and the application of devices can improve overall safety. We can help you verify that systems are operating within defined parameters and standards.
- Program lifecycle management and validation - following the safety lifecycle approach, which begins with the identification of risks or hazards. After we help you specify system requirements and design, install and validate your safety system, you can focus on maintenance and continuous improvement of the system. The lifecycle model is designed to help protect your investment and maintain the integrity of your safety system.
Asset and plant optimisation
An effective asset management strategy can help you improve equipment availability, boost OEE, and reduce your maintenance, repair and operations spend on a day-to-day basis. Asset management services can help you get the most from your operations, proactively address downtime issues and help manage risks.
By identifying process improvements, relying on dedicated specialists and using technology innovations and comprehensive data analytics, we can help you improve asset performance with asset modernisation and inventory services that go beyond basic repair services, offering you the following benefits:
- Reduce costs and improve reliability
- Increase uptime, decrease inventory and enable access to critical spares
- Improve processes and maximise productivity
- Identify, support and modernise aging assets
- Leverage data to optimise maintenance processes and systems.
Asset performance management services leverage analytics, alerts and alarms from intelligent devices to improve your asset availability.
Inventory services can help you:
- have ready access to the right spare parts when you need them
- reduce your MRO costs and improve maintenance decisions with MRO demand management
- improve your storeroom design and processes for continuous cost savings
- provide comprehensive inspection and testing to ensure the integrity of critical spare parts.
Asset modernisation services for legacy assets helps eliminate obsolescence risk and accelerate progress to The Connected Enterprise.
Asset performance management - reliability tools, assessments and performance monitoring can help you get the most from your assets and identify issues before they materialise into downtime events, using a scalable approach to service your performance and reliability demands.
Information infrastructure and security
As you move toward a Connected Enterprise, you may be challenged to integrate innovative technologies, improve the reliability and speed of your network, and maintain up-to-date protection against cyber and physical attacks. You may also need help identifying what parts of your network infrastructure need to be updated to support technology advances.
Through our services, we help you build a modern, secure, and reliable information infrastructure to connect your assets with people and information and improve your operational performance. We help you assess, design, and build a secure infrastructure – and then help protect and maintain it.
ACB modernisation: retrofits and upgrades
With ACB retrofit solutions available to facilitate the installation of a range of products and brands, as well as customising solutions to suit specific requirements, NHP can work within your existing switchboard environment to provide a cost-effective solution, resulting in an increase in system reliability, minimising production downtime and thereby lowering your operational costs. NHP’s ACB retrofit solutions are engineered according to relevant Australian and New Zealand standards and recognised industrial practices.
Power quality services
Our range of power quality services assist in determining your requirements through to ensuring your power quality system is optimised and delivering enduring results. Power Quality services available from NHP include:
- Power quality audits
- Commissioning services for NHP Power Factor Correction systems, Static Var Generators and Active Power Filters
- Periodic service and maintenance of NHP power quality systems
- Installation of NHP power quality systems.
Emergency breakdown assistance
NHP service provides you with options for 24/7/365 protection, ensuring that your assets continue to work for you. Our service technicians and engineers are on call, equipped to minimise downtime, and are here to provide you with rapid assistance when required.
Ensure you have the right parts, in the right place, at the right time with an Installed Based Evaluation
An Installed Base Evaluation™ provides better knowledge for you to make informed decisions, thanks to insights into your installed base. This is much more than simply counting parts. It’s a thorough analysis of your critical plant assets and their condition.
This service provides the knowledge needed to help you make data-driven decisions regarding the support and obsolescence management of your installed base assets. With an IBE, we can help you better understand and pinpoint your lifecycle risk by site, area, line, machine and panel. By optimising your maintenance, repair and operations, we’ll help ensure you have the right parts, in the right place, at the right time.
An IBE will enable:
• Thorough analysis - the IBE goes beyond simple part counting and provides a comprehensive analysis of critical plant assets and their condition;
• Data-driven decisions - the service equips customers with the knowledge needed to make data-driven decisions regarding the support and obsolescence management of installed base assets;
• Lifecycle risk identification – you’ll be able to pinpoint lifecycle risks by site, area, line, machine and panel, helping you to proactively manage and optimise your assets;
• Optimise maintenance and spares - by optimising maintenance, repair and operations, the IBE ensures you have the right parts in the right place, at the right time, reducing costs and increasing uptime;
• Inclusion of non-Rockwell Automation products - the IBE collects both Rockwell Automation and non-Rockwell Automation products, creating a comprehensive plant hierarchy model for the facility;
• Consultative approach - the IBE delivers analysis and recommendations through a consultative approach, helping you to understand the impact of equipment updates and spare parts management strategies;
• My Equipment dashboard - access to an online tool that provides easy to read dashboards with the ability to maintain the asset list as changes occur on site, giving an updated analysis to lifecycle risk and spare parts management.
Why choose NHP?
No matter how good a product may be, it is nothing without dedicated people to support that product. NHP is solely committed to servicing the needs of our customers. We bring together internationally recognised power distribution and automation products with local knowledge and expertise to deliver best practice services from concept design through to installation and after-sales service.
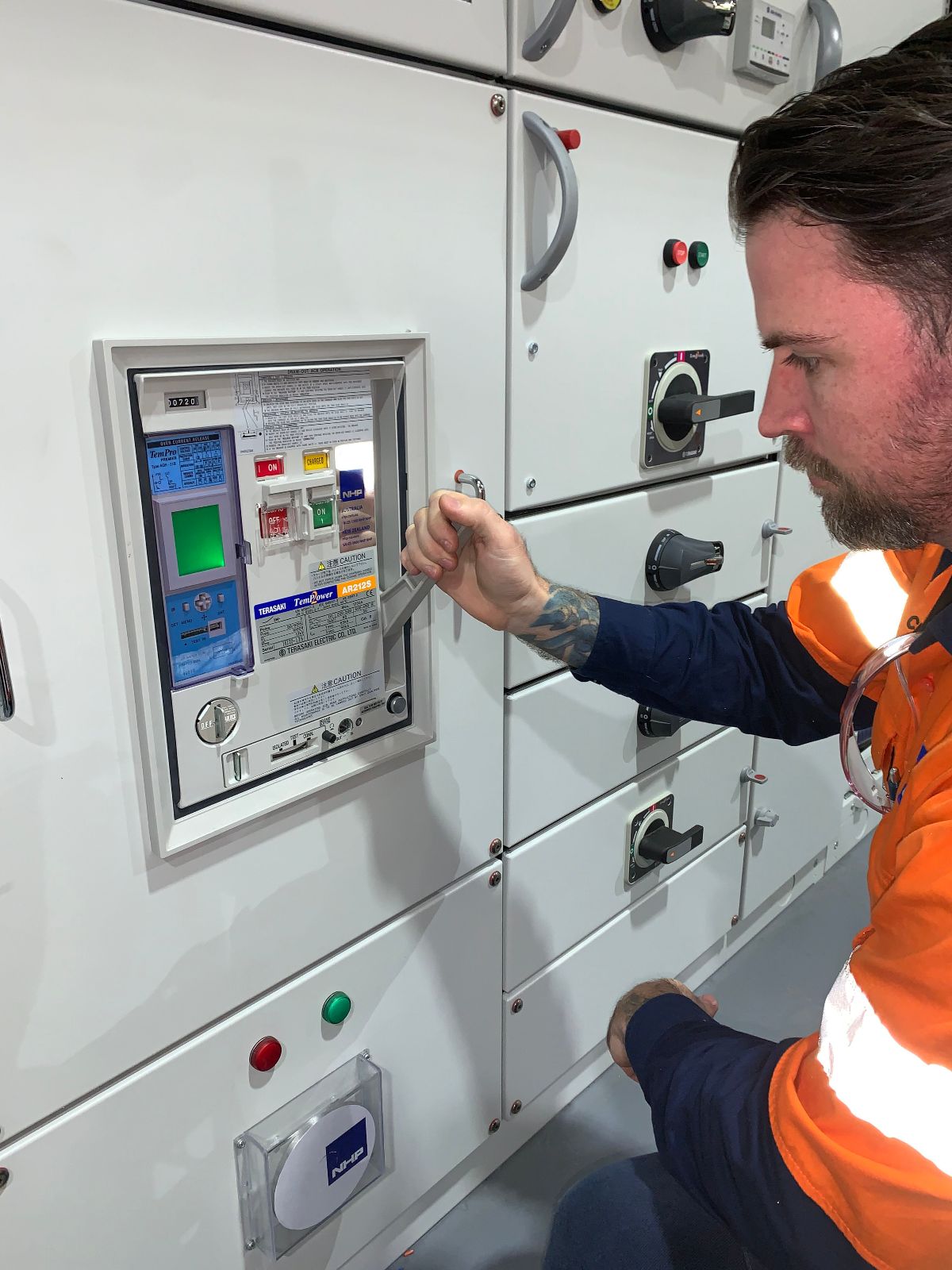