Today’s modern power distribution systems need to evolve to ensure that organisations can improve energy efficiency, reduce operating costs, and improve switchroom safety.
With such a large install base of aging legacy switchgear installed around the country, there is a continual need to review and assess the safety of and reliability of this equipment to ensure that you will not be unexpectedly left without power or worse experience a catastrophic failure that can potentially cause injury to employees.
Globally, health and safety regulators who investigate catastrophic electrical incidences have recognised that the pressure to avoid power shutdowns results in the neglect and deterioration of key electrical infrastructure like main switchboards and the critical components contained within them.
Over time, this neglect can cause significant failures due to switchgear contact corrosion, loose busbar connections and blocked air ventilation, inevitably leading to overheating and fire hazards. Conventional circuit breakers with electronic trip units do not offer any form of protection against overheating in the conductive path.
Within the context of an industrial plant’s electrical infrastructure, the wide spread deployment of smart, connected devices now allows end users to utilise a ‘Smarter Switchboard’ architecture to facilitate gathering and analysing critical data and provide real-time visibility and insight into how critical assets are performing. The outcome of this integrated solution can provide organisations with faster, more accurate information and enable them to make the right business decisions on optimising utilisation and extending the life time of their power distribution infrastructure.
A Smarter Switchboard architecture can help ensure continuity of power supply, minimise the service requirements of critical switchgear assets (such as circuit breakers) and enable real-time ‘maintenance health’ visualisation over a plant’s network.
Imagine we have a tier 4 data centre that provides 99.995% availability per year to its customers. To maintain such a high level of uptime/availability, the data centre’s power and cooling design requires layers of redundancy and furthermore, the ability to monitor the integrity of critical infrastructure. Any unplanned downtime will bring serious financial consequences and dissatisfied customers.
In this example the focus will be on the medium voltage/low voltage switchroom (1) and the Monitor and Control Centre (2) (see below).
Situation:
The low voltage switchboard contains a Smart Switchboard containing Terasaki TemPower2 air circuit breakers with integrated 3C overheating protection and data communication. The data centre’s Monitoring and Control Centre is using a visualisation health dashboard to monitor and report on mission critical intelligent devices.
Due to a ‘maintenance issue’ the forced cooling system in the switchroom starts to blow dust particles into the low voltage switchboard. Some of these contaminates eventually make their way inside one of the low voltage air circuit breakers internal contact system.
Over time, the electrical continuity of the air circuit breaker’s main contacts reduces due to the contamination and an abnormal contact overheating occurs.
Fortunately, the air circuit breaker’s 3C overheating protection detects the abnormal temperature within the contact set and activates the overheating alarm which is detected by the health dashboard and electrical maintenance contactors where notified who rectified the issue.
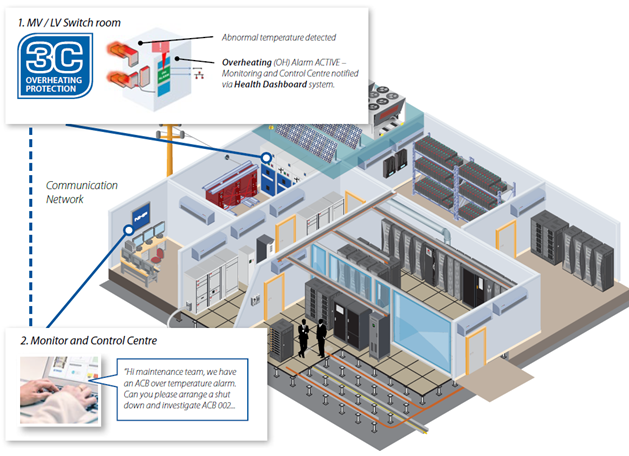
To find out more about how NHP’s Smarter Power Distribution architecture can unlock critical asset data to help drive your business performance to higher levels, contact your local NHP power distribution technology specialist today.